Distillation
The article below is provided by the Water Quality Association.
What is...Distillation?
|
Distillation is one of mankind's earliest forms of water treatment, and it is still a popular treatment solution throughout the world today. In ancient times, the Greeks used this process on their ships to convert sea water into drinking water. In far-eastern cultures, water was distilled for use in "Ranbiki" tea ceremonies. Today, distilled water is still used to convert sea water to drinking water on ships and in arid parts of the world, and to treat water in other areas that is fouled by natural and unnatural contaminants. Distillation is perhaps the one water treatment technology that most completely reduces the widest range of drinking water contaminants.
Not only is distillation one of the most effective forms of treatment, but it is also one of the easiest to understand: untreated water is converted into water vapor, which is then condensed back into liquid form. Most of the contaminants are left behind in the boiling chamber, with the condensed water being virtually contaminant-free. Anyone who has accidentally let a pot of water boil completely out on the stove is familiar with this process, and familiar with the crust of contaminants typically left behind after the water is gone.
In nature, this basic process is responsible for the hydrologic cycle. The sun causes water to evaporate from surface sources such as lakes, oceans, and streams. The water vapor eventually comes in contact with cooler air, where it re-condenses to form dew or rain. This process can be imitated artificially, and more rapidly than in nature, using alternative sources of heating and cooling.
|
|
|
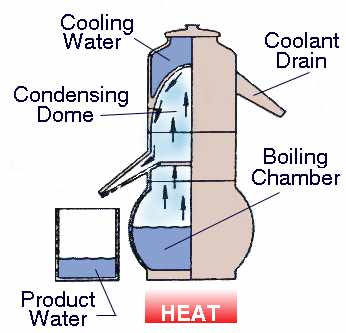 |
Sixteenth Century Clay Porcelain Distiller
|
Early distillation equipment was very simple in design: a pot of undrinkable water (or water unfit for a ceremonial, commercial, or medical purpose) would be heated over an open flame until it boiled, forming steam. The steam would then condense on a cool surface suspended above the pot. The condensed water droplets would then run off into a storage container for future use. Alternatively, sponges could be suspended above the pot to collect the treated water. While such systems were relatively inefficient, it tended to be quite adequate for the limited water treatment needs of the time.
The efficiency of the distillation process began to see improvements as distillation was adapted to commercially refine many different liquids such as alcohol, perfume, petroleum, and various solvents. Finally, population demands have strained water resources in the 20th century to the point where efficiently treating otherwise undrinkable sources of water for human consumption is increasingly important.
How Distillation Systems Work Several different types of distillation systems are available, the system chosen generally depending on the quantity of water required. Most households and businesses use inexpensive and effective single-stage distillers to provide less than a gallon, or up to 100 gallons, per day (gpd) of treated water. More economically efficient commercial distillation units produce up to 5,000 gallons per day, and use variations in steam pressure to help heat the water. Converting water into steam requires significant amounts of heat.
Most distillation units use either electricity, or, to a lesser extent, gas to generate the heat necessary. While it is difficult to get past the initial heating of the water, efficiency can be gained in keeping the process going by reusing the heated steam to preheat the incoming water.
Household Distillation The most common type of household and commercial distiller available is a basic, single-effect distiller. Single-effect distillers are simple in design, inexpensive, and effective. They are less efficient in energy use than some of the more elaborate processes used mainly for commercial treatment. Most single-stage distillers are relatively compact counter top or stand-alone units for use in the kitchen or office. These distillers can be either batch distillers, where a measured quantity of water is manually poured in, distilled, and collected; or plumbed distillers that automatically treat and maintain a constant supply of drinking water.
In a single-effect distiller, a heating element heats the water until it boils and eventually becomes steam. The steam is then drawn away from the boiling chamber, where it cools, condensing into highly treated distilled water. The contaminants in the original water are left behind in the boiling chamber.
|
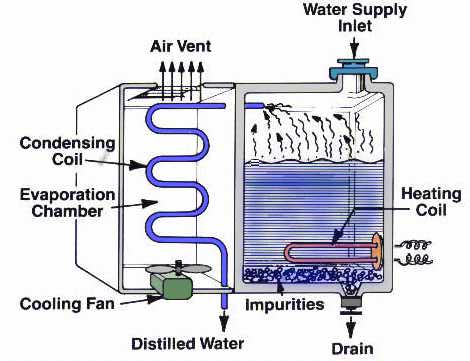 |
Modern Point-of-Use Distillation System
|
The condensing process is accomplished by using air or water to cool the steam. With some designs, the steam passes through coiled tubing which is either immersed in cool water, or cooled by a fan. (See above). In others, the roof of the boiling chamber is cone-shaped, with the cone being cooled by the non-heated water stored above it. Water droplets condense on the inside of the cone-shaped dome, and run down for collection in a drip pan. With some water-cooled systems, a portion of the heat lost as the steam is cooled and condensed can be reclaimed by channelling the heated cooling water into the boiling chamber. It is then replaced with fresh, cool water. The pre-heated water requires less new energy to convert it into steam. (See the WaterReview Technical Report "Efficiencies of Distillation Equipment" for more information on energy-conserving designs.)
While the distillation process alone is very effective, certain pesticides and contaminants like volatile organic compounds (VOCs) and radon convert into vapor readily, and can travel with the steam our of the boiling chamber. Almost all household distillers use special vents and carbon pre- and post-filters to effectively deal with these contaminants.
Distillation units do require some maintenance, which usually involves draining off the concentrated sediment and other contaminants that accumulate at the bottom of the boiling chamber. The walls of the chamber may also need to be cleaned of hard-water scale and other sediment that can accumulate. The required amount of cleaning depends greatly upon the initial quality of water used. Very hard water can produce heavy scaling in a relatively short period of time. If soft water is used, cleaning difficulties should be minimal. The carbon pre- and post-filters must be changed periodically as well.
Typical household distillers cost between $300 and $1,000 and produce water for as low as $.25 a gallon, energy and filter costs included. Look for the WQA Gold Seal (S-400) to find products that have been successfully tested by WQA to industry performance standards.
Commercial Distillers Many commercial operations use multiple-effect distillers, to provide from 75 to millions of gallons per day. These units typically contain a number of boiling chambers, with the first chamber being under increased pressure, and successive chambers having progressively decreasing pressure. This takes advantage of the fact that the greater the steam pressure, the higher the boiling point and temperature of the steam produced. The steam created in the first high-pressure chamber is "superheated" to a point well above the temperature needed to create steam in the lower-pressure chambers. As this superheated steam moves through tubes surrounding each of the succeeding boiling chambers, it "flash" vaporizes some of the cooler, lower-pressure water in each chamber. The flash vapor is then condensed into distilled water, as is the superheated steam when all of its heat energy is exchanged. The self-sustaining nature of this process can be quite efficient for large quantities of water, since only an electric or gas heating element is required for the first boiling chamber as an energy source.
A variation of the multiple-effect distiller concept is the vapor-compression distiller, which is typically used in commercial applications requiring between 25 and 5000 gallons per day. Vapor-compression water distillers also use high-pressure, superheated steam to boil water; however, they only use a single chamber. The water in the boiling chamber is initially converted to steam at normal pressures and temperatures by an electric or gas heating element. The steam then passes through an electric compressor; the compression causes it to become superheated. The superheated steam is then directed through tubes back into the boiling chamber, where it eventually takes over the boiling process, condensing into distilled water as the heat transfer occurs. These systems are typically more efficient than multi-stage units, since the energy required to operate the compressor is less than that required to heat water using a heating element. The greater efficiency usually brings with it a greater cost, as compared to multistage units.
Both multi-stage and vapor-compression distillers can incorporate various forms of filtration to make a broadly effective treatment system. These systems can provide water for such uses as commercial water bottling. Both systems also require water that is softened to be practical, to prevent debilitating scaling with resultant heat transfer losses and maintenance costs.
At the municipal level, both multi-stage and vapor-compression distillation can provide large quantities of distilled water for drinking use, and are especially used in distilling seawater for use in arid areas adjacent to the oceans.
What Distiller Units Treat Distillation is an effective process for producing highly treated drinking water. Distillation can significantly reduce levels of sediment, metals, and biological contaminants, which are unable to travel out of the boiling chamber with the steam. When combined with effective activated carbon filtration, contaminants like VOCs and radon can also be controlled. It is recommended that only units designed and tested for health-contaminant reduction be used for such purposes. These units, when combined with activated carbon filtration, can be used to effectively treat such contaminants as: - Arsenic
- Asbestos
- Atracine (Herbicide/pesticides)
- Benzene
- Fluoride
- Lead
- Mercury
- Nitrate
- Trichloroethylene (TCE)
- Trihalomethanes
- Radium
- Radon
- Biological contaminants (bacteria, viruses, and water-borne cysts like cryptosporidium)
A distillation system with activated carbon filtration can also be quite effective for treating aesthetic drinking water contaminants like chlorine or iron bacteria, which lead to unpleasant tastes, odors, or colors.
Conclusion Distillation is an effective water treatment technology for household and commercial use. It provides water with a distinct clarity, up to 98% free of impurities. Distillation units are continually being improved to increase efficiency and water output, making them increasingly popular and cost-effective for residential and commercial users alike.
-------------------------------------------------- This article first appeared in the WaterReview Technical Brief, (1995) Volume 10, No. 2; a publication of the Water Quality Research Council; Copyright 1995 by the WQA. All rights reserved.
|
|
|
|
Copyright 2005 by the Water Quality Association – All rights reserved.
Water Quality Association
International Headquarters & Laboratory
4151 Naperville Road
Lisle, IL 60532-3696
USA
630 505 0160, Fax 630 505 9637
info@wqa.org, www.wqa.org
|
|
|